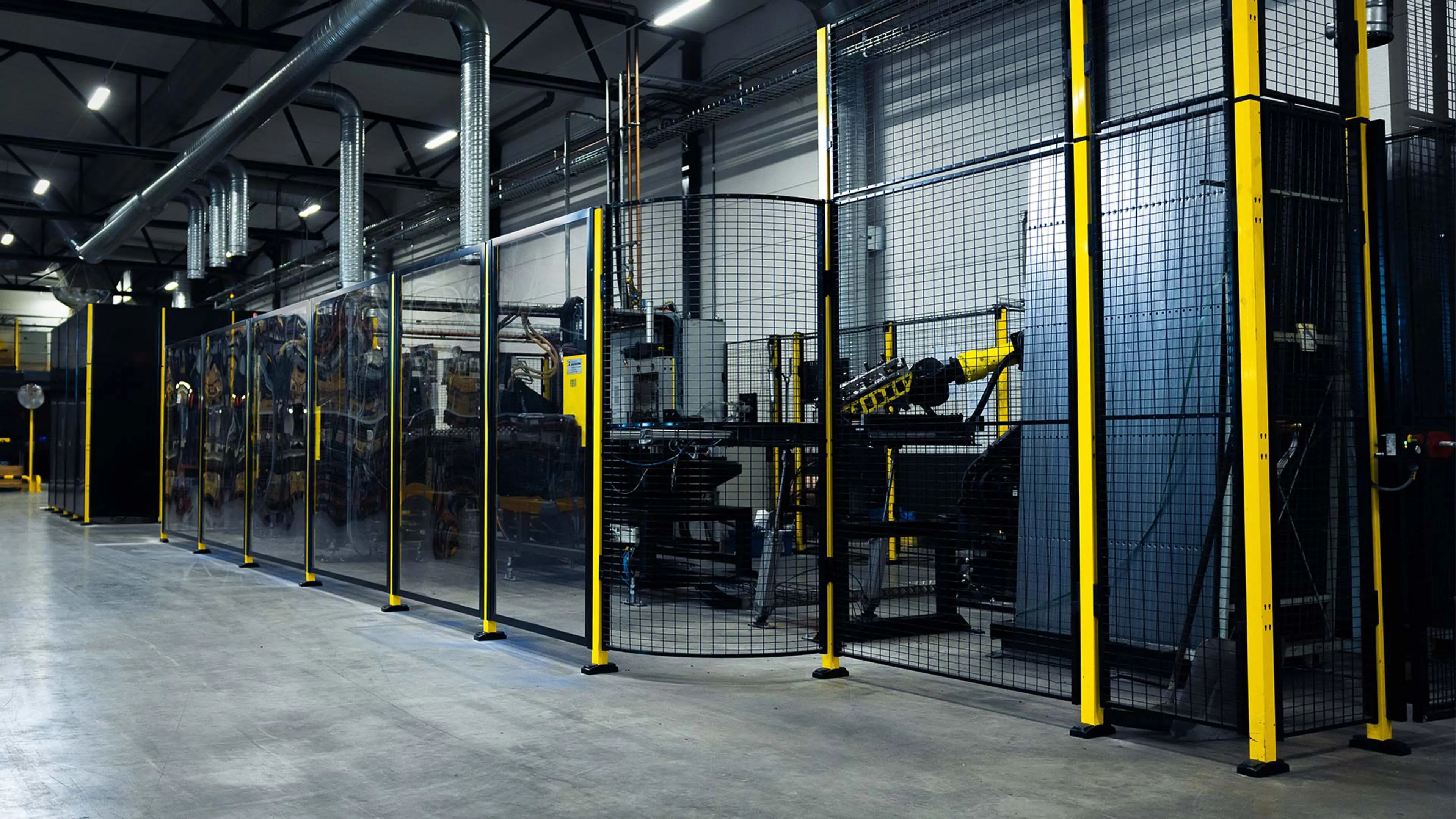
3.0
機械の安全性について
重要な機械安全規格をより簡単に理解できるように、次のセクションでは、これらの基準の主要なルールをわかりやすいイラストとともに紹介します。
基本原則
正しいリスクアセスメントを実施するには?
機械設計においては、機能性、効率、コストが主な焦点となることが多く、安全性は特にプロジェクトの初期段階で見落とされがちです。 リスクアセスメントの実施方法やその重要性について詳しく知りたい場合は、チャプター2.1「リスクアセスメント」をご参照ください。
早期にリスクアセスメントを実施することで、機械の安全性を向上
実際、プロジェクトの最終段階で追加された安全対策は、運用や効率に悪影響を及ぼすことが多いです。潜在的な危険については、最初から考え、できるだけ早い段階で解決策を考え始める方が良いです。
この危険を特定し、そのリスクの可能性を評価し、リスクを低減または排除するプロセスを「リスクアセスメント」と呼びます。
基本ステップ:
- 危険源を除去 可能な場合は危険源を除去します。
- 封じ込める 危険源を除去できない場合や、高い費用がかかる場合は、危険源を封じ込めます(人の立ち入りを禁じます)
- 停止する 人を危険源から常に離しておくことができない場合は、危険源の近くの人の存在を監視し、人が危害を受ける前に危険源を停止します。
過去には、エンジニアは安全に関する問題を体系的にアプローチすることはありませんでした。しかし、1990年代に製品安全に関する規制や基準が厳格化されてからは、「リスクアセスメント」が安全な製品と規制遵守への最も重要なステップとなっています。
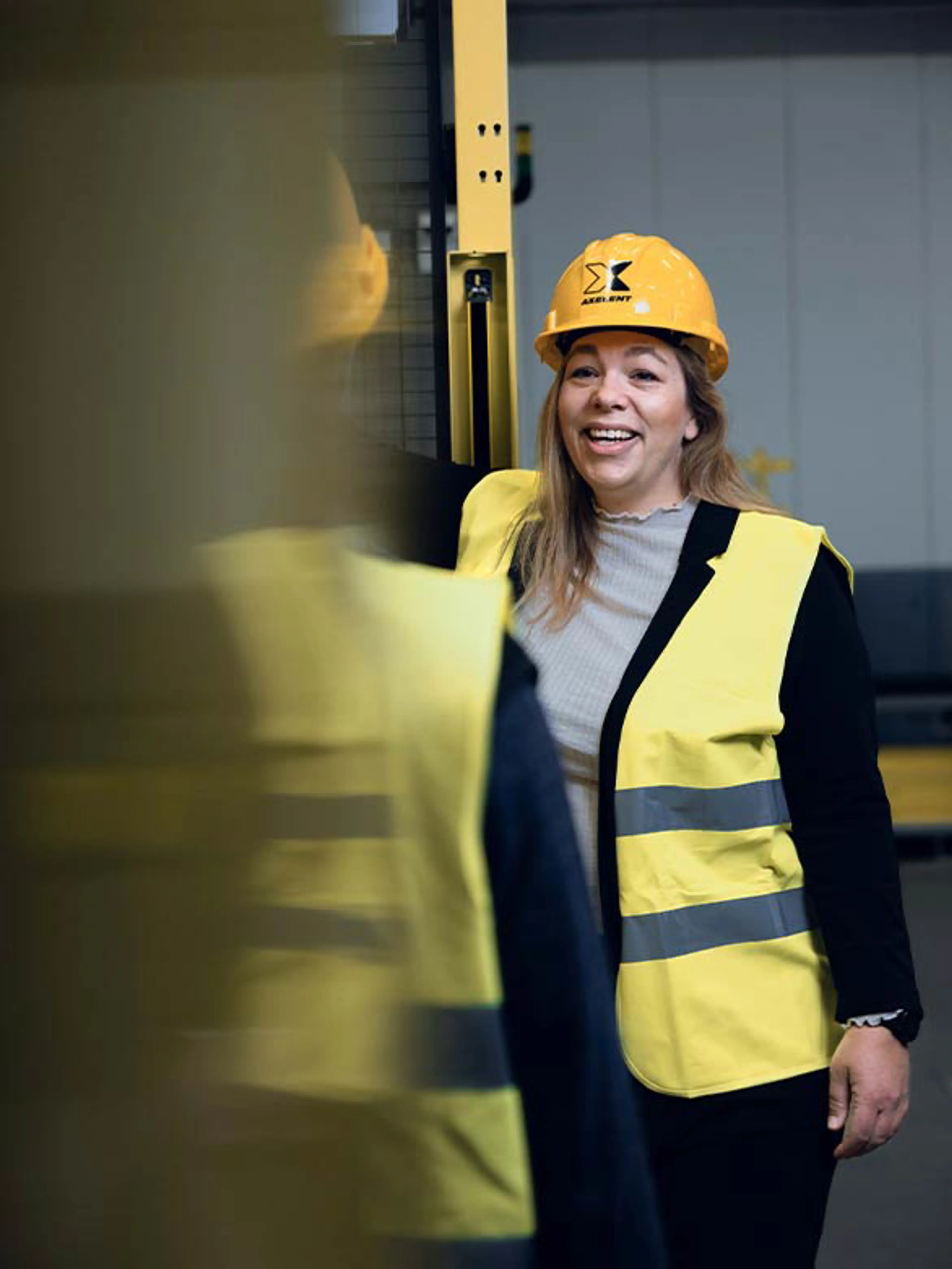
リスクアセスメントの5段階実施手順
多くの規則や安全基準では、5段階のリスク評価を求めています。
- 機械の限界を、意図された使用方法と潜在的な誤用を含めて特定する。
- 発生する危険とそれに関連する危険な状況を特定する。
- 可能なけがの重篤度とその発生確率を考慮してリスクを評価する。
- リスクを評価し、リスク低減が必要かどうかを判断する。
- 危険を排除するか、保護措置を講じてこれらの危険に関連するリスクを低減する。
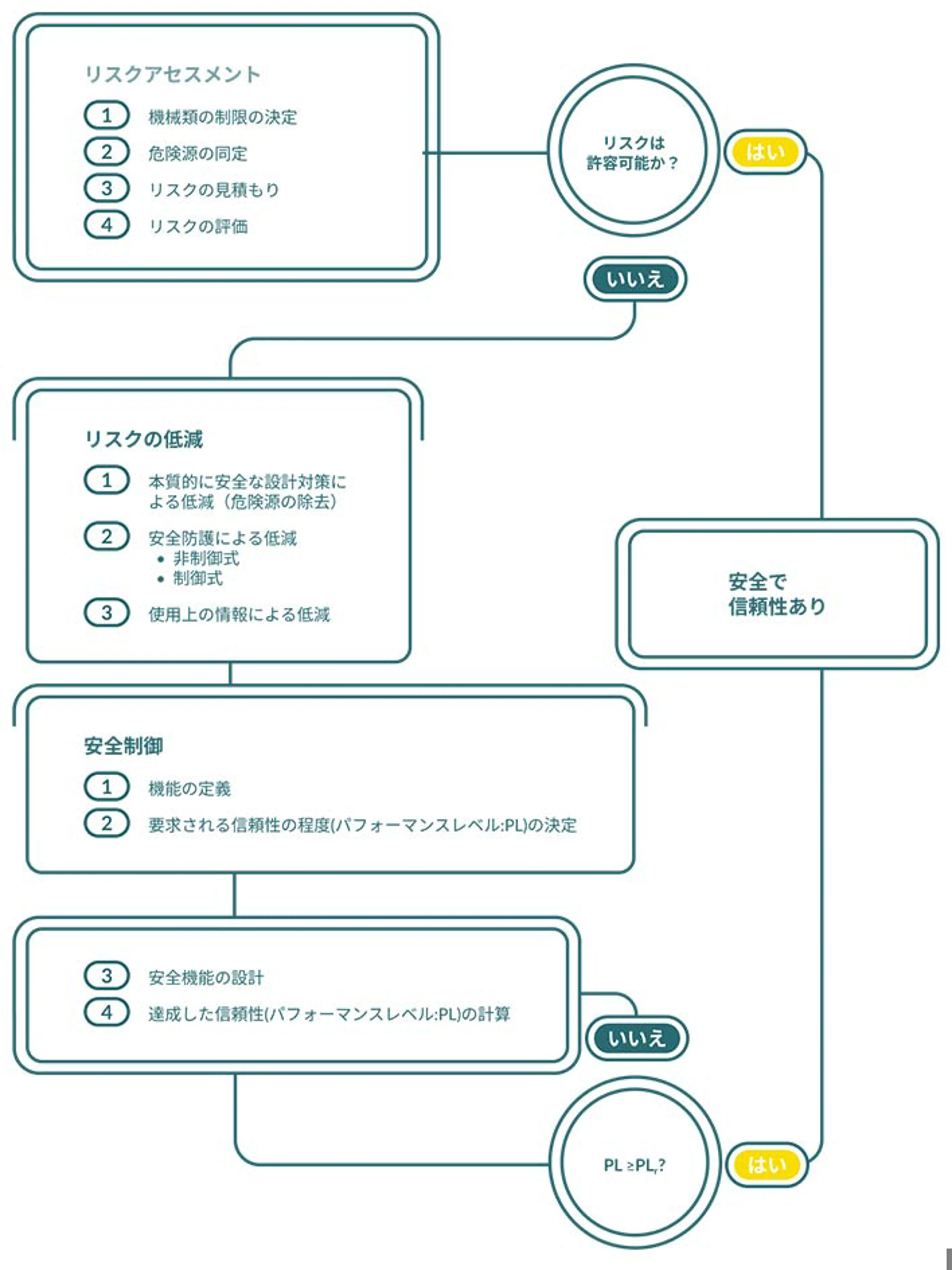
リスクアセスメントにおける各ステップの概要
機械の安全性と信頼性を確保するためには、徹底的なリスク評価プロセスを理解し、実施することが重要です。以下に、各ステップの詳細な内訳を示します。
リスクアセスメントを実施する
評価対象のタスクを定義
タスク:
オペレーターが機械にパレットを運び確認する
危険を探し、発生する事象を説明する
危険
稼働しているロボット:
- クラッシュ、せん断
- 衝突
危険の可能性
動いているロボットとパレットや機械のパーツにぶつかる危険性がある
安全対策の選定
安全対策:
ガードフェンスと保護装置(ILC)の組み合わせ
- 危険エリアは、意図的および偶発的なアクセスを防止するガードフェンスで囲まれています。
- アクセス用のドアが設けられており、これは可動式ガードとして機能します。
- 可動式ガードにはインターロックとガードロックが備えられており、危険エリア内のロボットおよび機械の動作が停止するまでドアが閉じられた状態を保持します。
- ドアが開いている、またはロックされていない限り、機械は起動できません。
- ドアスイッチには、緊急脱出用のロックが装備されている必要があります。
指令や規格から要件を割り当て
機械指令:
- 1.3.7 – 移動部に関連するリスク
- 1.4.2.1 – 固定ガード
- 1.4.2.2 – インターロック付き可動ガード
EN ISO 12100: 2010: sections 6.3.3.2.2 and 6.3.3.2.3
インターロック機能のパフォーマンスレベル(PL)を見つけるためにリスク見積り
インターロック機能のパフォーマンスレベル(PL)を見つけるためのリスク見積り
S – 危害の程度: 2
オペレーターはロボットによって重傷を負う可能性があり、致命的な傷害も考えられます。
F – 頻度と持続時間: 1
パレットは約1時間ごとに交換する必要があります。
P – 危害の予防: 2
ロボットは最大10 m/sの速度で移動し、回避はほぼ不可能です。
O – 発生の確率: 2
エビデンスはありません。
PLr: d